
ENERGY
Technical ceramics are able to continuously work under extreme temperatures of over 1000℃ which traditional materials such as plastic & metals are not capable of achieving. Due to the high working temperature, it is widely used in energy related applications like solid oxide fuel cells, refractories, foundry, heat dissipation and catalyst.


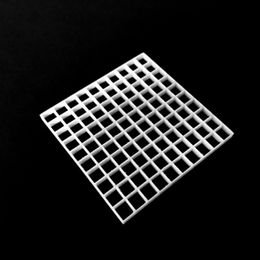
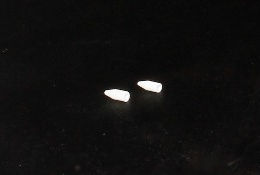
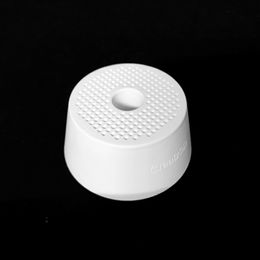




KEY PROPERTIES
KEY PROPERTIES
CUSTOMIZED
SINTERING SUPPORT
Heat treatment in metal injection molding (MIM) and ceramic injection molding (CIM) processes require customized support to prevent deformation. Due to freedom of design and fast delivery of parts, we have also provided sintering support to companies doing CIM and MIM.
CASTING CORE/INSERT
Turbine blades for the aerospace industry usually require complex channels inside them. The core/inserts are used to create the channels during casting. There is a need to optimize the performance from time to time, but the cores are too complex to be produced traditionally. However, ceramic AM is a good solution.
CASTING SHELL
The investment casting process in making the refractory shell mould is based on the wax model. With ceramic AM, ceramic shells can be printed directly to serve as the casting shell. Shells made by ceramic AM can also cast more complicated parts compared to investment casting.
CATALYTIC SUPPORT
Ceramic honeycomb or lattice can be used as catalytic support for exhaust purifier in automotive. With AM, the freedom of design in lattice and honeycomb structure, allows for the improved efficiency of the catalyst .
HEAT SINKS
Alumina is a good heat conductor and with AM, we are able to increase the surface area significantly by designing internal grooves and curved fins. This increases the efficiency of heat dissipation, this kind of design cannot be produced by traditional ceramic manufacturing processes.